In modern manufacturing, the application of 2000W fiber laser welding machines for welding aluminum metals is becoming increasingly widespread. However, to ensure welding quality and safety, the following key matters need to be noted.
1. Surface treatment before welding
The oxide film on the surface of aluminum metal can seriously affect the welding quality. Thorough surface treatment must be carried out to remove the oxide film, oil stains and other impurities. When a certain automotive parts enterprise welded the aluminum frame, due to the neglect of surface treatment, a large number of pores and cracks appeared in the weld, and the qualification rate dropped sharply. After improving the treatment process, the qualification rate rose to more than 95%.
2. Selection of Appropriate Welding Parameters
Welding parameters such as laser power, welding speed and focus position are of great importance. For aluminum plates with a thickness of 2 - 3mm, a power of 1500 - 1800W is more appropriate; for those with a thickness of 3 - 5mm, 1800 - 2000W is suitable. The welding speed should match the power. For example, when the power is 1800W, a speed of 5 - 7mm/s is ideal. The focus position also affects the welding effect. The focus for thin plates is on the surface, while for thick plates, it needs to be deeper inside.
3. Control of Heat Input
Aluminum metal has a high thermal conductivity and is prone to heat loss, which affects the weld penetration and strength. Precise control of heat input is required. For example, when an aerospace enterprise welded aluminum parts, poor control of heat input led to incomplete fusion of the weld. The problem was solved after optimizing the process.
4. Application of Shielding Gas
Appropriate shielding gas can prevent weld oxidation and porosity. Argon, helium or their mixtures are commonly used, and the flow rate and blowing direction should be adjusted properly. Research shows that an argon flow rate of 15 - 20 L/min and an appropriate blowing direction can reduce porosity.
In the future, it is expected that higher-power and more intelligent laser welding equipment will emerge, and new welding processes and materials will also promote its wide application. In conclusion, only by following these precautions, accumulating experience and optimizing the process can the advantages of laser welding be exerted to contribute to the development of the manufacturing industry.
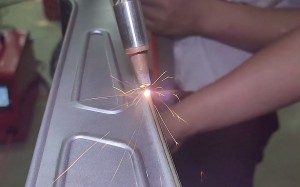
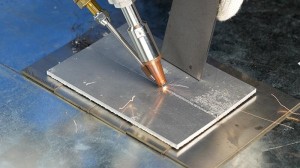
Post time: Jul-12-2024