In the era of continuous growth in energy demand and rapid changes in battery technology nowadays, the battery manufacturing industry has put forward increasingly higher requirements for the precision and efficiency of the production process. As an advanced welding method, the galvanometer welding technology is emerging in the field of battery manufacturing by virtue of its unique advantages.
Galvanometer welding technology is a laser-based high-precision and high-speed welding method. Its working principle is to guide the high-energy-density laser beam to perform rapid scanning and welding on the surface of the workpiece by controlling the rapid and precise movement of the galvanometer.
The galvanometer welding technology can achieve an extremely high welding precision of up to 0.01 millimeters. The emergence of the galvanometer welding technology has brought revolutionary changes to the battery manufacturing industry. Its non-contact welding method avoids the pollution and damage caused by physical contact, and at the same time can concentrate the laser energy in a very small area in an instant to achieve efficient and precise welding.
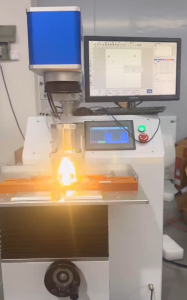
The characteristics of this technology are remarkable: 1. Non-contact welding:
1.It completely avoids direct contact with the workpiece, thereby reducing workpiece deformation and surface damage caused by physical contact, and at the same time reduces the risk of contamination to the workpiece.
2. High energy density: The energy of the laser beam can be concentrated in a very small welding area in an instant to achieve rapid melting and connection, greatly improving the welding efficiency.
3. Fast response: The galvanometer system can adjust the position of the laser beam at an extremely high speed, making the welding process more flexible and able to adapt to various complex welding trajectories and shapes.
The galvanometer welding technology has indispensable applications in multiple key links of battery manufacturing. In the welding of battery tabs, as a key component for current transmission inside the battery, the connection quality between the tabs and the battery body directly affects the performance of the battery. A well-known lithium-ion battery manufacturer adopted the advanced galvanometer welding technology to weld the tabs during the production process. By precisely controlling the welding parameters, a seamless connection between the tabs and the battery body was achieved, effectively reducing the resistance and improving the charging and discharging efficiency of the battery. According to actual tests, the charging and discharging cycle life of the battery after galvanometer welding has been extended by more than 20%. In terms of the sealed welding of battery cases, the advantages of galvanometer welding are even more irreplaceable. The sealing performance of the battery case is directly related to the safety and service life of the battery. For example, when producing power batteries, the galvanometer welding technology is used to weld the battery case, achieving high-strength welds and zero leakage. After strict pressure tests and immersion tests, the welded battery case can withstand a pressure of up to 10 atmospheres, and no electrolyte leakage occurs during long-term use. Furthermore, in the connection of battery modules, galvanometer welding also plays a key role. Battery modules are usually composed of multiple single batteries, and the welding quality of the connectors between the modules directly affects the performance and stability of the entire module. Through the galvanometer welding technology, the connectors between the battery modules can be precisely welded to ensure the uniform distribution of current within the module and improve the consistency and stability of the entire module.
To sum up, the galvanometer welding technology has demonstrated huge application potential and advantages in the field of battery manufacturing. With the continuous progress of battery technology and the continuous improvement of market requirements for battery performance, the advantages of high precision, high efficiency, and high stability of the galvanometer welding technology will be further exerted.
It can be foreseen that in the future battery manufacturing industry, the galvanometer welding technology will become one of the mainstream welding processes, promoting the battery industry to develop in the direction of higher quality, higher performance, and lower cost. For battery manufacturing enterprises, actively introducing and applying the galvanometer welding technology will be a key measure to enhance their own competitiveness and achieve sustainable development.
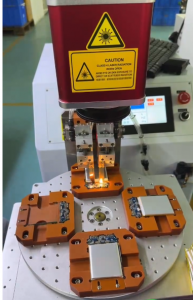
Post time: Jun-24-2024