In the field of modern industrial manufacturing, laser welding, as a high-precision and high-efficiency welding technology, is receiving increasing attention. For potential customers of handheld laser welders, understanding the differences in laser welding of different steel materials is crucial for achieving the ideal welding effect and ensuring welding quality.
First, let's get to know the common steel materials, such as carbon steel, stainless steel and alloy steel.
Carbon steel is one of the most common steel materials, and its different carbon contents will affect its performance. Low-carbon steel has good weldability. Medium-carbon steel requires more cautious handling during welding, while high-carbon steel is more difficult to weld.
Stainless steel has good corrosion resistance and oxidation resistance. Common types include austenitic stainless steel, ferritic stainless steel and martensitic stainless steel. Their composition and microstructure determine their welding characteristics.
Alloy steel is a type of steel that acquires specific properties by adding alloying elements, such as strength, toughness and wear resistance.
Laser welding has extensive applications and significant advantages on these different steel materials. Its high precision can achieve very small weld widths and depths, thereby reducing the heat-affected zone and improving the welding quality. The high energy density enables fast welding speed and greatly improves efficiency. Moreover, the weld seam of laser welding is beautiful and has high strength, which can meet various strict industrial requirements.
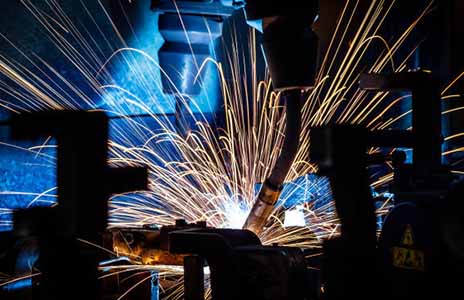
Next, focus on comparing and analyzing the key differences of different steel materials during the laser welding process.
In terms of temperature distribution, carbon steel has a relatively high thermal conductivity, so heat is transferred quickly and the temperature distribution is relatively uniform. However, stainless steel has a lower thermal conductivity and is prone to generating local high temperatures during welding, requiring more precise control.
The deformation situations also differ. Generally speaking, the deformation of carbon steel is relatively small, while stainless steel, due to its larger coefficient of thermal expansion, is prone to larger deformation during the welding process.
In terms of composition changes, during the welding process of alloy steel, the distribution and burning loss of alloying elements will have an important impact on the welding quality.
For different steels, here are some optimal laser welding parameters and technical suggestions.
For carbon steel, a higher welding speed and moderate laser power can be adopted to reduce heat input and avoid excessive welding.
Stainless steel requires a lower welding speed and higher power. At the same time, pay attention to the use of shielding gas to prevent oxidation.
The welding parameters of alloy steel need to be adjusted according to the specific alloy composition to ensure the uniform distribution of alloying elements.
In conclusion, laser welding has broad prospects in steel processing. The presence of laser welding can be seen in fields such as automotive manufacturing, aerospace, electronic equipment, and medical devices.
For example, in automotive manufacturing, laser welding is widely used in the connection of vehicle body structures, improving the strength and safety of the vehicle body. In the aerospace field, for the welding of high-strength alloy steel components, laser welding can ensure high precision and quality.
To enable you to obtain better welding results in actual operations, we recommend that you use our [brand name] handheld laser welder. It features advanced laser technology, stable performance, and convenient operation, and can meet your welding needs for different steel materials. Whether you are a small processing plant or a large manufacturing enterprise, our product will be a powerful assistant for you to improve welding quality and efficiency.
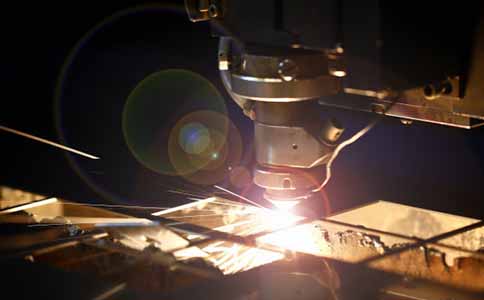
Post time: Jun-26-2024