In today's welding field, handheld laser welding machines have gradually become mainstream with their outstanding performance. Compared with traditional welding machines, they have ten significant advantages.
The first is high precision and high-quality welding. The weld seams of handheld laser welding machines are narrow and uniform, with a minimal heat-affected zone, ensuring highly stable and precise welding quality. For example, in automotive manufacturing, it can make component connections more secure and the appearance more exquisite, while traditional welding is prone to problems such as uneven weld seams and pores. In the manufacturing of precision instruments, the high-precision demand for handheld laser welding machines is particularly evident, as it can guarantee the accuracy and reliability of the instruments.
Secondly, the welding speed is significantly improved. It can complete a large amount of welding work in a short time, greatly enhancing production efficiency. In metal furniture manufacturing, where traditional welding takes several hours, the handheld laser welding machine can finish the job in just a few tens of minutes. For instance, a large metal furniture factory significantly shortened the production cycle after adopting the handheld laser welding machine, meeting the rapid market demand.
Furthermore, flexibility and portability stand out. It is small in size and light in weight, and the operator can easily handle various angles and positions in complex environments by holding it, unlike traditional welding machines that are limited by space. For example, at pipeline maintenance sites, the handheld laser welding machine can easily reach the narrow interior of the pipeline for welding.
Low energy consumption and energy conservation and environmental protection are also among its advantages. The energy consumption during the welding process is low, meeting current environmental protection requirements, and long-term use can save a significant amount of energy costs.
There is also higher weld seam strength, capable of withstanding greater loads and pressures, and performing exceptionally well in fields with extremely high strength requirements such as aerospace. For example, for some components of aircraft engines, the strength is significantly enhanced after using handheld laser welding.
The operation is simple and easy to master. Workers can become proficient with short-term training, and compared to traditional welding machines, the requirements for the operator's experience and skills are lower.
A wide range of weldable materials, whether it's metals, alloys, or plastics, can be welded easily. Traditional welding machines have limitations in this aspect.
The weld seam is aesthetically pleasing and requires no post-processing. The weld seam surface is smooth and flat, unlike traditional welding that often requires additional grinding and polishing processes. In the manufacturing of high-end electronic product casings, the handheld laser welding machine can directly provide aesthetically pleasing weld seams without the need for post-processing.
High stability and reliability. The advanced control system and stable laser source enable it to operate stably for a long time, with a low frequency of faults and maintenance.
Finally, it can reduce production costs. Considering all aspects, long-term use can significantly reduce enterprise costs.
To sum up, these ten advantages of handheld laser welding machines make them stand out in the welding field. Although the initial investment may be higher, in the long run, the economic benefits brought are considerable. With technological development and cost reduction, it is bound to occupy a more important position in the future.
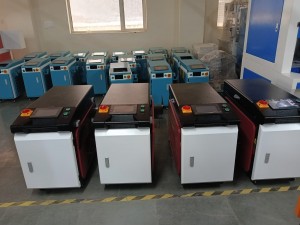
Post time: Jun-21-2024